Welcome to My Blog!
Before we dive into the content, I’d love for you to join me on my social media platforms where I share more insights, engage with the community, and post updates. Here’s how you can connect with me:
Facebook:https://www.facebook.com/profile.php?id=61565500692293
Now, let’s get started on our journey together. I hope you find the content here insightful, engaging, and valuable.
Table of Contents
Introduction
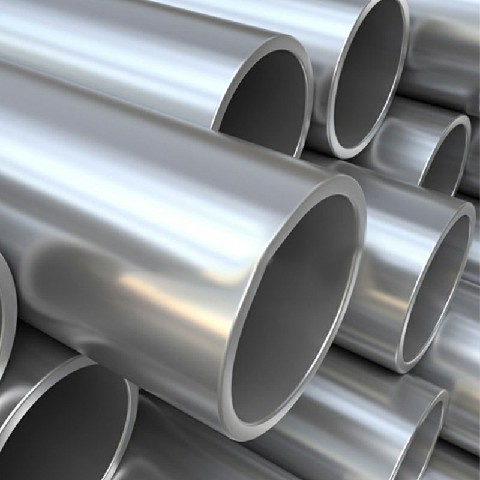
Alloy seamless steel pipes are an essential material in various industries such as oil and gas, automotive, chemical, and construction. Known for their remarkable strength and long-lasting durability, these pipes are used in applications where other materials would fail under pressure, temperature, or corrosive environments. The seamless nature of these pipes eliminates the weak points found in welded alternatives, offering superior performance and reliability. This blog will delve into why alloy seamless steel pipes are so durable, examining factors like material properties, manufacturing processes, and their applications across different industries.
What Are Alloy Seamless Steel Pipes?
Alloy seamless steel pipes are steel pipes made from high-quality alloy materials such as chromium, molybdenum, nickel, and other elements that enhance the steel’s strength, corrosion resistance, and overall durability. These pipes are manufactured through a process where a solid billet is heated and then formed into a pipe shape by piercing and elongating the material. The lack of seams, or welds, is a key feature of alloy seamless steel pipes, making them more robust and capable of handling higher stress levels than welded pipes.
The primary distinction between alloy seamless steel pipes and welded pipes lies in the construction. Alloy seamless pipes are produced from a single billet of metal, while welded pipes are created by welding a longitudinal seam. This process gives alloy seamless steel pipes greater uniformity, fewer weak spots, and an overall stronger structure. These pipes are ideal for high-pressure applications, where strength and reliability are essential.
How Alloy Seamless Steel Pipes Are Manufactured
The manufacturing process of alloy seamless steel pipes plays a crucial role in their durability. Understanding this process helps highlight the key factors that contribute to the pipe’s longevity and structural integrity.
- Steel Preparation: Alloy seamless steel pipe manufacturing begins with high-quality steel billets. These billets are heated to a temperature that makes the steel malleable and easier to work with. The quality of the raw material is critical to ensuring the pipe’s durability in its final form.
- Piercing: After heating, the steel billet is pierced using a punch to create the hollow center of the pipe. This step forms the initial shape of the pipe, which will then be further elongated and refined.
- Elongation: The pierced billet is elongated into the desired length using rollers and mechanical force. This process creates the pipe’s final size and ensures the walls of the pipe are even and consistent throughout.
- Heat Treatment: To further enhance the pipe’s mechanical properties, it undergoes heat treatment. This step is crucial for improving the hardness, strength, and resistance to high temperatures, making alloy seamless steel pipes more suitable for demanding applications.
- Finishing: Once the pipe is elongated and heat-treated, it is polished, coated, and inspected for quality. The final inspection ensures the pipes meet the required standards for durability, strength, and resistance to corrosion. This step also includes non-destructive testing such as ultrasonic testing to identify any potential defects that may compromise the pipe’s performance.
By eliminating the need for welding, alloy seamless steel pipes are more structurally sound and capable of withstanding extreme conditions, such as high pressure, temperature, and corrosive environments.
Durability Factors of Alloy Seamless Steel Pipes
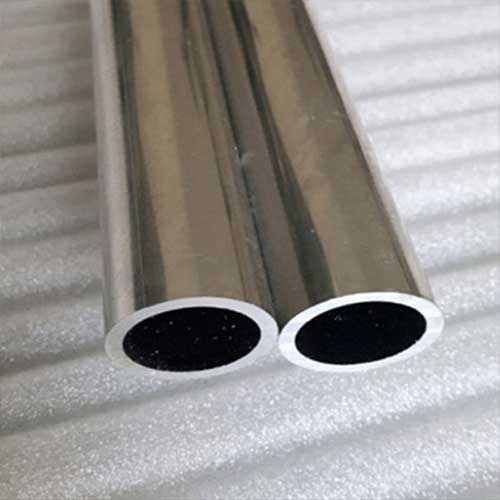
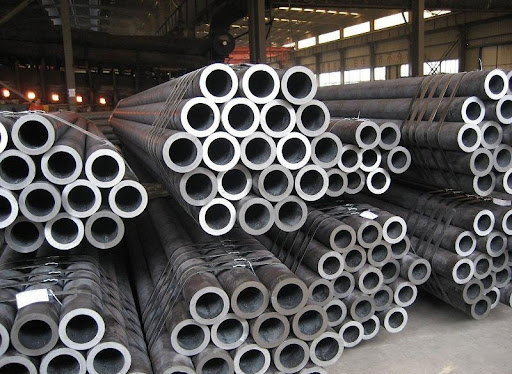
Material Properties and Composition
The composition of alloy seamless steel pipes is a major factor in their durability. These pipes are made from a blend of high-strength materials that enhance their mechanical properties. Key alloying elements include:
- Chromium: Adds resistance to corrosion and oxidation. This makes alloy seamless steel pipes suitable for harsh chemical environments or applications exposed to high moisture levels.
- Nickel: Increases the toughness and strength of the pipe, even under sub-zero temperatures or when exposed to fluctuating temperatures.
- Molybdenum: Helps improve the pipe’s resistance to high-temperature creep and increases its strength under high pressure.
- Vanadium: Increases the pipe’s toughness and resistance to wear and tear, making it more durable under high-stress conditions.
These alloying elements not only enhance the steel’s overall strength but also improve its resistance to environmental factors like corrosion, oxidation, and wear. As a result, alloy seamless steel pipes can perform well in extreme conditions, extending their lifespan and reducing the need for frequent replacements.
Pressure and Temperature Resistance
One of the primary reasons alloy seamless steel pipes are so durable is their ability to withstand high pressures and extreme temperatures. The seamless construction and high-quality materials make these pipes resistant to internal and external pressure, which is particularly important in industries like oil and gas or power generation.
In addition to withstanding high pressures, alloy seamless steel pipes also perform well at high temperatures. The addition of elements like chromium and molybdenum enhances the pipe’s ability to resist thermal expansion and contraction, ensuring that it maintains its shape and strength when exposed to temperature fluctuations. This characteristic is particularly valuable in industries like power plants, where pipes often carry hot steam and other high-temperature fluids.
Corrosion Resistance
Corrosion is one of the primary causes of failure in metal pipes. Alloy seamless steel pipes are designed to resist corrosion, which significantly enhances their durability. The alloying elements, particularly chromium, form a passive oxide layer on the surface of the pipe, preventing further corrosion from occurring. This makes alloy seamless steel pipes ideal for use in environments where moisture, chemicals, or harsh weather conditions are prevalent.
Industries like petrochemicals, marine engineering, and construction benefit from the corrosion-resistant properties of alloy seamless steel pipes, which are exposed to corrosive elements such as saltwater, acids, and other harsh chemicals.
Enhanced Structural Integrity
The seamless nature of these pipes plays a critical role in their durability. Without welds or seams, alloy seamless steel pipes are less prone to failure due to structural weaknesses. Welds are often the point of failure in welded pipes, but alloy seamless steel pipes do not have this vulnerability. The uniformity of the pipe’s structure means that stress and pressure are distributed evenly, allowing it to withstand higher loads without the risk of cracking or breaking.
This superior structural integrity makes alloy seamless steel pipes suitable for high-stress applications such as structural support in bridges, buildings, and heavy equipment.
Applications of Alloy Seamless Steel Pipes
Alloy seamless steel pipes are used in a wide range of applications where their durability and reliability are paramount. Some key industries and applications include:
- Oil and Gas: Alloy seamless steel pipes are essential in transporting oil, gas, and other fluids over long distances in pipelines. These pipes must withstand high pressures, extreme temperatures, and corrosive environments.
- Power Generation: In power plants, alloy seamless steel pipes are used in boilers, heat exchangers, and other equipment that operates at high temperatures and pressures. The durability of these pipes ensures the efficient and safe operation of power plants.
- Chemical Processing: Alloy seamless steel pipes are used to transport chemicals, liquids, and gases in refineries and chemical plants. Their resistance to corrosion makes them ideal for handling aggressive substances.
- Automotive and Aerospace: These pipes are used in exhaust systems, hydraulic systems, and structural components of vehicles and aircraft due to their strength, heat resistance, and durability.
- Construction: Alloy seamless steel pipes are used in heavy-duty construction projects, particularly for structural support where high strength and resistance to stress are needed.
Advantages of Alloy Seamless Steel Pipes
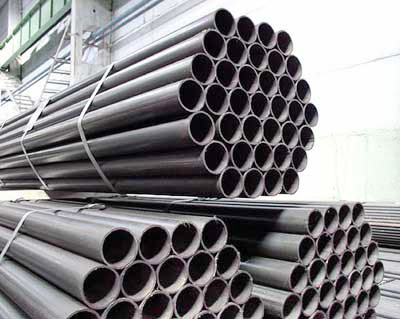
Advantage | Description |
---|---|
High Strength | Alloy seamless steel pipes offer superior tensile strength, making them ideal for use in high-pressure environments. |
Corrosion Resistance | The presence of chromium and other elements in alloy pipes provides excellent resistance to corrosion, making them suitable for aggressive environments. |
Uniformity in Design | The seamless design ensures that the pipes are consistent in wall thickness and structural integrity, reducing the risk of failure. |
Temperature and Pressure Resistance | Alloy seamless steel pipes can withstand extreme temperatures and pressures without compromising their structural integrity. |
Longer Service Life | Thanks to their durability and resistance to environmental factors, alloy seamless steel pipes generally last longer than welded pipes, reducing maintenance needs. |
Conclusion
Alloy seamless steel pipes are durable because of their material composition, seamless construction, and ability to withstand extreme conditions. Their resistance to pressure, temperature, and corrosion makes them ideal for applications in the oil and gas, power generation, automotive, chemical processing, and construction industries. These pipes are built to last, offering superior strength and reliability when compared to welded alternatives.
The combination of high-quality alloys and advanced manufacturing techniques ensures that alloy seamless steel pipes provide unmatched performance, reducing maintenance costs and extending the lifespan of critical infrastructure. As industries continue to demand more durable materials, alloy seamless steel pipes will remain a top choice for engineers and manufacturers around the world.
FAQ
Why are alloy seamless steel pipes better than welded pipes?
Alloy seamless steel pipes have no welds, which means they are structurally stronger and can handle higher pressures and temperatures without risk of failure. This makes them more durable than welded pipes, especially in high-stress applications.
Can alloy seamless steel pipes be used in high-temperature environments?
Yes, alloy seamless steel pipes are designed to withstand high temperatures. The presence of alloying elements like chromium and molybdenum enhances their ability to resist thermal expansion and maintain structural integrity in high-temperature environments.
What industries use alloy seamless steel pipes?
Alloy seamless steel pipes are used in industries like oil and gas, power generation, automotive, chemical processing, and construction due to their strength, corrosion resistance, and ability to withstand extreme conditions.
How long do alloy seamless steel pipes last?
The durability of alloy seamless steel pipes can extend for decades, depending on the environment and application. Their resistance to corrosion and pressure means they require fewer replacements and less maintenance over time.
Are alloy seamless steel pipes more expensive than welded pipes?
Although alloy seamless steel pipes may have a higher initial cost due to the manufacturing process, their superior durability and longer service life can make them more cost-effective in the long run, especially in high-demand applications.