مرحبًا بك في مدونتي!
قبل أن نتعمق في المحتوى، أود أن تنضموا إليّ على منصات التواصل الاجتماعي الخاصة بي حيث أشارك المزيد من الأفكار وأتفاعل مع المجتمع وأنشر التحديثات. إليك كيف يمكنك التواصل معي:
فيسبوك : فيسبوكhttps://www.facebook.com/profile.php?id=61565500692293
والآن، لنبدأ رحلتنا معًا. آمل أن تجدوا المحتوى هنا ثاقباً وجذاباً وقيّماً.
جدول المحتويات
مقدمة
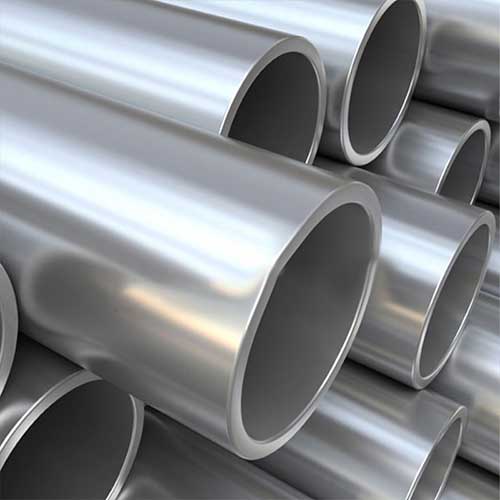
كيف يتم تصنيع الأنابيب غير الملحومة؟ يتم إنتاج الأنابيب غير الملحومة بدون أي لحامات، مما ينتج عنه هيكل متصل وموحد. وتمنحها هذه الطبيعة غير الملحومة خصائص ميكانيكية ممتازة، مما يجعلها مثالية لتطبيقات الضغط العالي والاستخدامات الهيكلية الحرجة
تبدأ عملية تصنيع الأنابيب غير الملحومة باختيار المواد الخام عالية الجودة، تليها سلسلة من خطوات التصنيع المصممة بعناية لضمان دقتها وأدائها. سنتطرق في هذه المدونة إلى تفاصيل هذه العمليات، مع التركيز على العمليات والتقنيات المستخدمة في إنتاج الأنابيب غير الملحومة.
عملية تصنيع الأنابيب غير الملحومة
ينطوي إنتاج الأنابيب غير الملحومة على تحويل قضبان الصلب الصلبة إلى أنابيب مجوفة من خلال طرق مختلفة. وتشمل التقنيات الأساسية الثقب الدوار والبثق وعملية مانسمان. كل طريقة لها خطواتها ومعداتها الفريدة من نوعها، ولكن جميعها تهدف إلى إنتاج أنابيب بدون طبقات ملحومة.
اختيار المواد الخام
الخطوة الأولى في تصنيع الأنابيب غير الملحومة هي اختيار المواد الخام عالية الجودة. وعادةً ما يتم اختيار قضبان أو قضبان الصلب الصلبة لتكوينها الموحد وسلامتها الهيكلية. وتعمل هذه القضبان كأساس لإنتاج الأنابيب التي تلبي معايير الصناعة الصارمة.
ما أهمية ذلك:
- يضمن أن المنتج النهائي يتمتع بخصائص ميكانيكية متسقة.
- يقلل من احتمالية حدوث عيوب أثناء مراحل التصنيع اللاحقة.
- يوفر قاعدة موثوقة لإنتاج أنابيب قادرة على تحمل الضغوط ودرجات الحرارة العالية.
تسخين القضبان
وبمجرد اختيار القضبان، يتم تسخينها إلى درجة حرارة محددة لجعلها قابلة للطرق لمزيد من المعالجة. ويتم هذا التسخين عادةً في فرن موقد دوّار، حيث يتم تسخين القضبان بشكل موحد إلى درجات حرارة تبلغ حوالي 1200 درجة مئوية (2190 درجة فهرنهايت).
ما أهمية ذلك:
- يسهل التشوه بسهولة أثناء عمليتي الثقب والاستطالة.
- يضمن توحيد خصائص المواد في جميع أنحاء البليت.
- إعداد البليت لتحويله بسلاسة إلى أنبوب مجوف.
الثقب الدوار
بعد التسخين، تخضع القضبان إلى عملية ثقب دوارة، وهي خطوة حاسمة في تكوين الجزء المجوف من الأنبوب. وفي هذه العملية، يتم تغذية القضبان المسخّنة بين بكرتين منحرفتين تدوران في نفس الاتجاه. ويتم وضع نقطة ثقب، تُعرف أيضًا باسم المغزل، في المنتصف. وعندما يمر البليت من خلال البكرات، يخترق المغزل مركزه مشكلاً غلافًا مجوفًا.
ما أهمية ذلك:
- الشروع في إنشاء أنبوب مجوف غير ملحوم من قطعة حديدية صلبة.
- يحدد الأقطار الداخلية والخارجية الأولية للأنبوب.
- يمهد الطريق لمزيد من عمليات الاستطالة والتحجيم.
الاستطالة والتحجيم
بعد الثقب الدوراني، يخضع الغلاف المجوف للاستطالة لتحقيق الطول المطلوب وسُمك الجدار المطلوب. ويتم تحقيق ذلك من خلال مطاحن الدرفلة المختلفة، مثل مطحنة السدادة أو مطحنة المغزل، حيث يتم تمديد الغلاف بشكل أكبر وتقليل قطره.
ما أهمية ذلك:
- تنقيح أبعاد الأنبوب لتلبية متطلبات محددة.
- يحسّن الخواص الميكانيكية من خلال محاذاة البنية الحبيبية.
- ضمان سمك وقطر موحد للجدار على طول الأنبوب.
المعالجة الحرارية
وبعد الاستطالة، تخضع الأنابيب لعمليات المعالجة الحرارية مثل التطبيع والتبريد والتلطيف. تعمل هذه المعالجات على تخفيف الضغوط الناتجة أثناء التصنيع وتعزيز الخواص الميكانيكية للأنابيب.
ما أهمية ذلك:
- يحسن من قوة الأنابيب وصلابتها وليونتها.
- يصقل البنية المجهرية لتحسين الأداء تحت الضغط.
- التأكد من أن الأنابيب تفي بمعايير الصناعة للخصائص الميكانيكية.
الاستقامة والفحص
بعد المعالجة الحرارية، يتم تقويم الأنابيب باستخدام معدات متخصصة لتصحيح أي تشوهات. ثم تخضع بعد ذلك لعمليات فحص صارمة، بما في ذلك طرق الاختبار غير المدمرة مثل الاختبار بالموجات فوق الصوتية واختبار التيار الدوامي للكشف عن أي عيوب داخلية أو سطحية.
ما أهمية ذلك:
- يضمن خلو الأنابيب من العيوب التي قد تؤثر على الأداء.
- يضمن دقة الأبعاد والاستقامة.
- يؤكد الامتثال لمعايير الصناعة ومواصفاتها.
التقطيع والتشطيب
وتشمل الخطوات النهائية قطع الأنابيب إلى أطوال محددة وتطبيق التشطيبات السطحية حسب الحاجة. وقد يشمل ذلك عمليات مثل الشطف، أو الخيوط، أو الطلاء لإعداد الأنابيب للاستخدامات المخصصة لها.
ما أهمية ذلك:
- تخصيص الأنابيب للاستخدامات المحددة ومتطلبات التركيب.
- يعزز مقاومة التآكل وطول العمر من خلال الطلاء المناسب.
- توفر منتجات جاهزة للاستخدام تلبي مواصفات العميل.
الجدول: نظرة عامة على الأنابيب غير الملحومة عمليات التصنيع
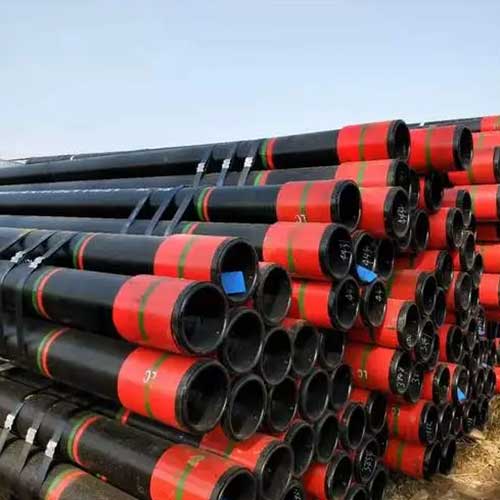
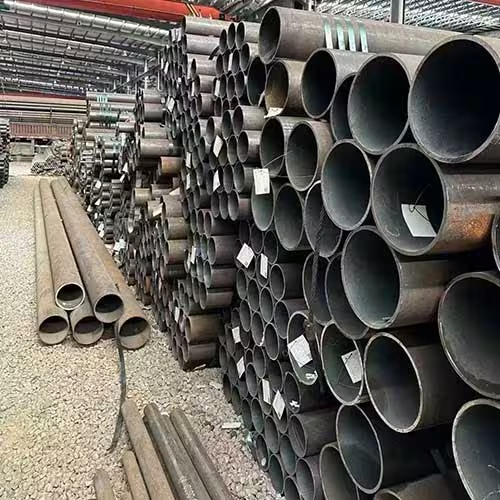
كيف يتم تصنيع الأنابيب غير الملحومة؟ يلخص الجدول التالي الخطوات الرئيسية المتبعة في تصنيع الأنابيب غير الملحومة:
الخطوة | الوصف |
---|---|
اختيار المواد الخام | اختيار قضبان الفولاذ عالية الجودة للحصول على تركيبة موحدة وسلامة هيكلية. |
التدفئة | تسخين القضبان بشكل موحد إلى حوالي 1,200 درجة مئوية لتسهيل التشوه. |
الثقب الدوار | ثقب القضبان المسخّنة باستخدام بكرات مسننة ومغزل لإنشاء غلاف مجوف. |
الاستطالة والتحجيم | تمديد الغلاف المجوف وتصغيره لتحقيق الأبعاد المطلوبة باستخدام ماكينات الدرفلة. |
المعالجة الحرارية | تطبيق عمليات مثل التطبيع والتلطيف لتعزيز الخواص الميكانيكية. |
الاستقامة والفحص | تصحيح التشوهات وفحص العيوب باستخدام طرق الاختبار غير المتلفة. |
التقطيع والتشطيب | التقطيع حسب الأطوال المحددة وتطبيق التشطيبات السطحية مثل الخيوط أو الطلاء. |
يقدم هذا الجدول لمحة موجزة عن عملية تصنيع الأنابيب غير الملحومة، مع تسليط الضوء على الخطوات الحاسمة التي تضمن إنتاج أنابيب عالية الجودة.
مزايا الأنابيب غير الملحومة
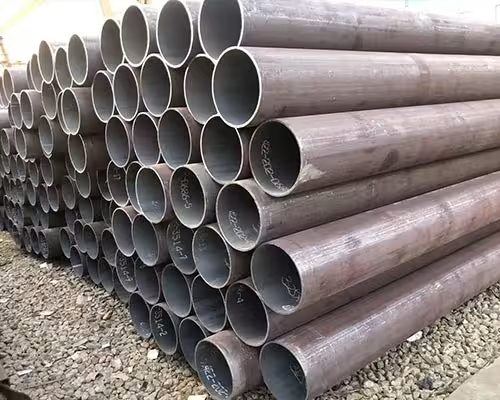
توفر الأنابيب غير الملحومة العديد من المزايا مقارنةً بنظيراتها الملحومة، مما يجعلها خيارات مفضلة في مختلف التطبيقات. وتنبع هذه المزايا من عملية تصنيعها الفريدة وخصائصها الهيكلية المتأصلة.
تعزيز القوة والمتانة
إن عدم وجود طبقات ملحومة يزيل نقاط الضعف المحتملة، مما يوفر قوة موحدة في جميع أنحاء الأنبوب. وهذا يجعل الأنابيب غير الملحومة قادرة على تحمل الضغوط والإجهادات العالية.
مقاومة فائقة للتآكل
وتتميز الأنابيب غير الملحومة بهيكل موحد بدون وصلات ملحومة، مما يقلل من مخاطر نقاط بدء التآكل. ويعزز هذا التوحيد من مقاومتها للبيئات المسببة للتآكل.
تحسين التعامل مع الضغط
يسمح التركيب المتجانس للأنابيب غير الملحومة بالتعامل مع الضغوط الداخلية الأعلى، مما يجعلها مناسبة لتطبيقات الضغط العالي في صناعات مثل النفط والغاز.
صفات جمالية ووظيفية أفضل
تتميز الأنابيب غير الملحومة بمظهر سلس وموحد، والذي غالباً ما يكون مفضلاً في التطبيقات المعمارية. كما أن تجانسها يسهل تركيبها وصيانتها.
الخاتمة
كيف يتم تصنيع الأنابيب غير الملحومة؟ يكشف فهم كيفية صناعة الأنابيب غير الملحومة عن العمليات الدقيقة التي ينطوي عليها إنتاج هذه المكونات الأساسية. من اختيار المواد الخام عالية الجودة إلى تطبيق تقنيات تصنيع دقيقة، تضمن كل خطوة إنتاج أنابيب تلبي معايير الأداء والجودة الصارمة.
سواء كانت تستخدم في نقل السوائل في قطاع النفط والغاز، أو توفير السلامة الهيكلية في البناء، أو دعم التطبيقات ذات درجات الحرارة العالية في محطات الطاقة، فإن الأنابيب غير الملحومة هي عنصر أساسي في البنية التحتية والتصنيع الحديث.
الأسئلة الشائعة
ما الفرق بين سلس والأنابيب الملحومة؟
يكمن الاختلاف الرئيسي في عملية التصنيع. حيث يتم إنتاج الأنابيب غير الملحومة من قضبان صلبة يتم ثقبها لإنشاء أنبوب مجوف بدون أي طبقات ملحومة. في المقابل، يتم تصنيع الأنابيب الملحومة عن طريق دحرجة الفولاذ المسطح في شكل أسطواني ثم لحام الحواف معًا. وبسبب عدم وجود لحامات، تكون الأنابيب غير الملحومة أقوى بشكل عام وأكثر مقاومة للضغط والتآكل.
ما أهمية عملية تصنيع الأنابيب غير الملحومة؟
إن فهم كيفية صنع الأنابيب غير الملحومة يساعد المشترين والمهندسين على تقييم مدى ملاءمتها لمختلف التطبيقات. تضمن العملية التوحيد والقوة الفائقة ومقاومة الضغط العالي ودرجة الحرارة العالية. وتكتسب هذه المعرفة أهمية خاصة في صناعات مثل النفط والغاز، حيث يمكن أن يكون لأعطال الأداء عواقب مالية كبيرة على السلامة والسلامة.
ما هي المواد المستخدمة عادةً في إنتاج الأنابيب غير الملحومة؟
تصنع الأنابيب غير الملحومة عادةً من الفولاذ الكربوني وسبائك الفولاذ والفولاذ المقاوم للصدأ. يتم اختيار كل مادة بناءً على الاستخدام المقصود للأنبوب. على سبيل المثال، يُستخدم الفولاذ الكربوني على نطاق واسع للأغراض الصناعية العامة، بينما يُفضل استخدام الفولاذ المقاوم للصدأ في البيئات المسببة للتآكل. اختيار المواد أمر بالغ الأهمية ويرتبط مباشرة بكيفية صنع الأنابيب غير الملحومة وكيفية أدائها.
هل يمكن تخصيص الأنابيب غير الملحومة لتطبيقات محددة؟
نعم، يمكن تصنيع الأنابيب غير الملحومة بأطوال وسماكات جدران وأقطار مختلفة بناءً على مواصفات العميل. بالإضافة إلى ذلك، تسمح معالجات ما بعد المعالجة مثل التلدين والتبريد وطلاء السطح بمزيد من التخصيص. تتيح معرفة كيفية تصنيع الأنابيب غير الملحومة اتخاذ قرارات أفضل فيما يتعلق بتصميم المنتج النهائي وأدائه.
هل الأنابيب غير الملحومة هي الخيار الأفضل دائماً؟
ليس دائمًا. في حين أن الأنابيب غير الملحومة توفر مزايا من حيث القوة ومقاومة الضغط، إلا أنها قد تكون أكثر تكلفة ويصعب الحصول عليها لمواصفات معينة. قد تكون الأنابيب الملحومة كافية للتطبيقات منخفضة الضغط أو غير الحرجة. ومع ذلك، في السيناريوهات التي تكون فيها الموثوقية والتجانس ومقاومة الضغط ذات أهمية قصوى، فإن فهم كيفية صنع الأنابيب غير الملحومة يجعلها حجة مقنعة لاختيارها على البدائل الملحومة.