مرحبًا بك في مدونتي!
قبل أن نتعمق في المحتوى، أود أن تنضموا إليّ على منصات التواصل الاجتماعي الخاصة بي حيث أشارك المزيد من الأفكار وأتفاعل مع المجتمع وأنشر التحديثات. إليك كيف يمكنك التواصل معي:
فيسبوك : فيسبوكhttps://www.facebook.com/profile.php?id=61565500692293
والآن، لنبدأ رحلتنا معًا. آمل أن تجدوا المحتوى هنا ثاقباً وجذاباً وقيّماً.
جدول المحتويات
مقدمة
Understanding the carbon steel pipe temperature range is critical in industries where temperature extremes are part of daily operations. Whether you’re designing a steam pipeline, a chemical process system, or a chilled water network, knowing how hot or cold your pipes can get without compromising safety or performance is essential.
This article is your go-to guide for everything you need to know, helping you make informed decisions based on real-world conditions.
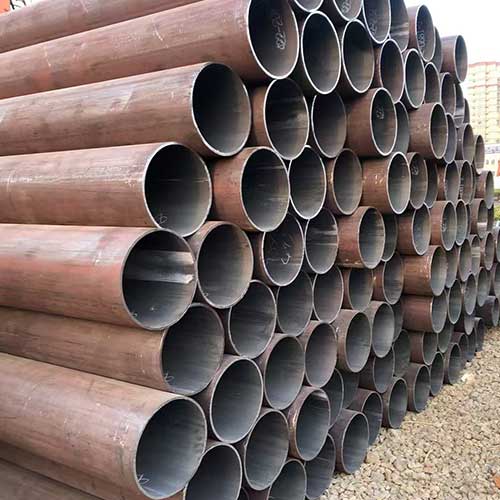
What Defines the أنابيب الصلب الكربوني نطاق درجة الحرارة
The temperature range for carbon steel pipes is largely determined by the material’s chemical makeup and physical properties. Carbon steel typically contains up to 0.30% carbon, which provides strength but can lead to brittleness at low temperatures. The inclusion of manganese and other elements influences heat resistance and durability under pressure.
Industrial standards like ASME B31.1, B31.3, and ASTM A106 or A53 help define safe stress levels at various temperatures. As heat increases, the tensile and yield strengths of carbon steel drop, which limits how much pressure the pipe can handle. This is why knowing your system’s exact temperature profile is so important during the design phase.
Another factor is the presence of coatings, linings, or insulation. While these can protect against corrosion and reduce heat loss, they don’t fundamentally extend the base material’s temperature range. In high-stakes environments like power generation or oil refining, it’s crucial to match your pipe material to both thermal and mechanical stresses.
Typical Carbon Steel Pipe Temperature Limits
Let’s break down the general guidelines for low and high temperature limits. On the low end, standard carbon steel begins to lose ductility below –30 °C. For systems expected to operate below that, a low-temperature grade—tested to –46 °C—is typically required.
On the upper end, most carbon steel pipes are suitable up to 425 °C before strength degradation becomes a risk. If your system needs to run hotter, like 500 °C or more, you’ll need to switch to alloy steels such as chrome-moly variants.
Here’s a simplified reference table:
Service Condition | Min Temp | Max Temp | Notes |
---|---|---|---|
Cryogenic Service | –46 °C (–50 °F) | –29 °C (–20 °F) | Use only certified low-temp grades |
Ambient Conditions | –29 °C (–20 °F) | 120 °C (248 °F) | Standard carbon steel application |
High-Temp Water/Steam | 120 °C (248 °F) | 425 °C (797 °F) | Use ASME stress tables for safe limits |
Extreme Heat Services | 425 °C (797 °F) | 550 °C+ (1022 °F) | Requires alloy steel for long-term strength |
According to ASME data, for example, ASTM A106 Grade B can withstand up to 425 °C safely, assuming the correct pressure derating is applied. Beyond this, the material enters a creep regime, where even small stresses can lead to long-term failure.
Real-World Applications and Their Temperature Ranges
In steam power systems, carbon steel is used for piping where temperatures typically range from 200 °C to 400 °C. This makes Grade B pipe a common choice, as it offers the right balance of strength and affordability. However, high-stress loops or superheated sections may need upgraded alloys.
In oil and gas refineries, pipelines carry hot liquids and gases at 350 °C or higher. In these cases, the carbon steel pipe temperature range might be exceeded, prompting the use of chrome-moly materials. Process engineers have to calculate not just the steady-state temperature, but also spikes during startup or shutdown.
On the other end, chilled water systems or HVAC applications deal with cold temperatures, often down to –10 °C or lower. Here, carbon steel performs reliably if corrosion is managed and proper insulation is in place.
Factors That Influence Temperature Range Suitability
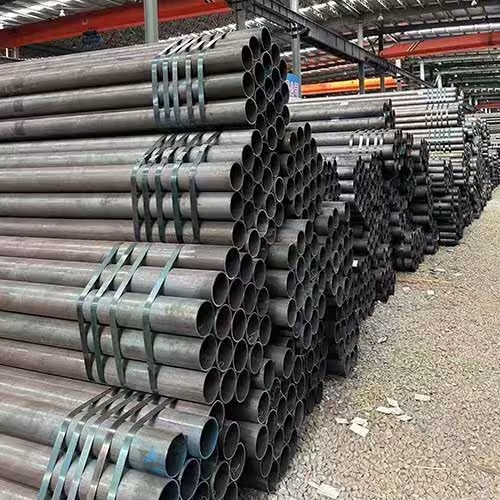
Design temperature is not the same as operating temperature. Codes often require that the pipe be rated for a higher “design” value to account for unexpected spikes. If your process runs at 370 °C, your design might be set at 400 °C just to be safe.
Another important factor is pressure-temperature derating. As temperature increases, the strength of carbon steel falls. At 400 °C, ASTM A106 Grade B has 30–40% less strength than at room temperature, according to ASME B31.3 data.
Thermal expansion must also be considered. Long runs of pipe expand significantly when exposed to heat. Without expansion joints or flexible loops, that movement can cause stress and failure over time. The right supports and guides are key.
How to Select the Right Pipe for Your System
Start by defining the highest and lowest temperatures your pipe will experience. Then, identify the standard that applies—ASTM A106, A53, or a similar grade. Look up the allowable stress at your design temperature and calculate whether your system will stay within those limits under pressure.
If your system operates in extreme cold, make sure your material has been tested for impact resistance at the expected low temperature. If it will run in continuous high-heat service above 425 °C, it’s time to look at alloy steels instead.
Also factor in the application. A hot water distribution system won’t need the same specs as a superheated steam line. Ask: Will this be in continuous use? Are thermal cycles frequent? Is downtime costly? These answers will guide your selection.
Inspection and Maintenance Under Temperature Stress
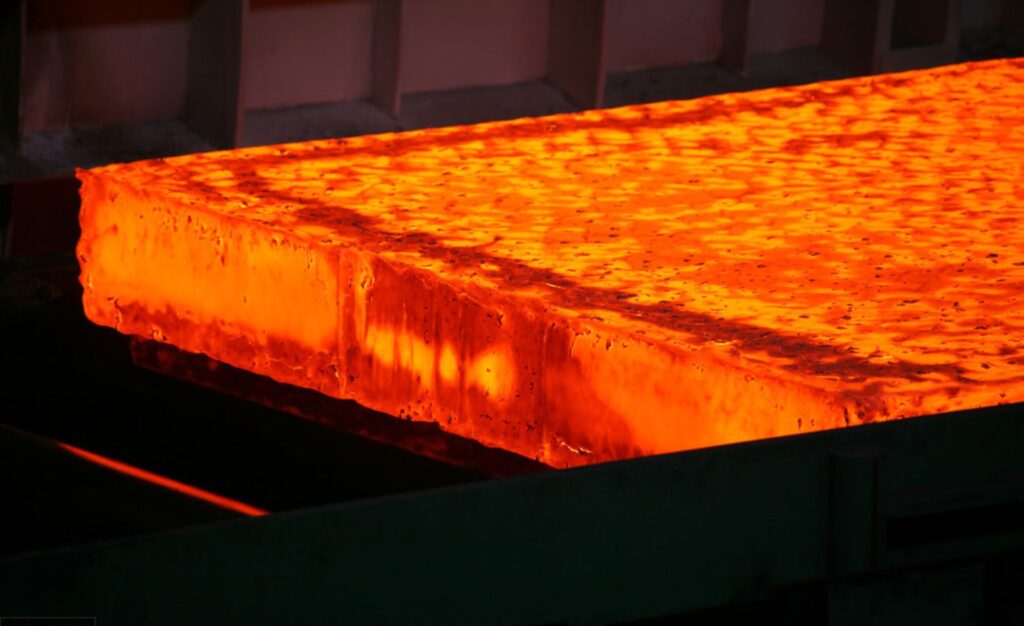
Even the right material can fail without proper maintenance. At elevated temperatures, the main concern is creep—gradual deformation under stress. That’s why long-term monitoring and inspection are vital in heat-heavy industries like power generation.
In cold environments, brittle fracture is a risk, especially if the material hasn’t been impact-tested for low-temperature service. Regular ultrasonic or radiographic testing can identify thinning walls or internal flaws before they lead to problems.
Weld zones are another critical point. The area around welds, known as the heat-affected zone, can behave differently than the pipe body. Ensuring consistent weld quality, and applying pre- or post-weld heat treatment as required, helps keep everything within safe performance margins.
الخاتمة
Choosing the right carbon steel pipe means more than just picking a size. You need to understand the carbon steel pipe temperature range, along with how your system behaves under thermal stress. Every degree matters when safety and performance are on the line.
Standard carbon steel handles most industrial temperatures, but for extreme heat or cryogenic use, specialized grades or even alloyed materials are necessary. Know your standards, verify the application requirements, and plan for long-term maintenance.
If you’re planning a system or retrofitting an existing one and want expert help on material selection, stress ratings, or thermal design—get in touch with us. We’re here to help you engineer with confidence.
الأسئلة الشائعة
What is the maximum temperature carbon steel pipe can handle?
Most standard carbon steel pipes, like ASTM A106 Grade B, can safely handle up to 425 °C. Beyond that, their strength diminishes, and alloyed steels become necessary.
Can carbon steel be used in sub-zero environments?
Yes, but only specific low-temperature grades of carbon steel. These are tested to ensure they don’t become brittle below –30 °C, with many certified to –46 °C.
Does pipe insulation affect temperature limits?
Insulation helps reduce heat loss and protect from freezing but doesn’t change the pipe’s inherent temperature range. You still need to select materials based on the actual service temperature.
How do I know when to use alloy steel instead of carbon steel?
If your design temperature exceeds 425 °C or the system is subject to long-term stress at high heat, switching to a chrome-moly alloy like 1¼Cr–½Mo is often required.
Are there standard codes I can reference?
Yes. Refer to ASME B31.3 for process piping or B31.1 for power piping. Also consult ASTM standards like A106 or A53 for material grades and allowable stress values by temperature.